3. Chain ink roller. The role of the ink roller is to level the ink in both the circumferential and axial directions. Only in this way can it be ensured that the ink volume of the printing plate is always even, and the effect of the ink stringing effect directly affects the uniformity of the ink on the printing plate. The following is a detailed analysis of the process of ink stringing.
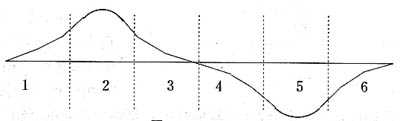
The ink fountain roller runs from left to right and from right to left. At the transition point from left to right or from right to left, the speed at which the ink string roller moves in the axial direction must be zero. Therefore, no ink can be produced at these two points. In the left-to-right or right-to-left process, the speed of axially converging of the ink roller gradually increases from zero to maximum and decreases from zero to maximum. The higher the speed of the shaft string, the better the effect of ink stringing. Obviously, the ink stringing effect in the middle place is the best. The pulsation of the serigraph roller is generally driven by an eccentric which drives the oscillating mechanism, so the speed change is approximately sinusoidal, as shown in Figure 3.2.
A series of reciprocating ink can be divided into six zones. Obviously, the ink stringing effect of the two zones and the five zones is the best, and the effect of the other four zones is similar. Therefore, the two zones and the five zones should be used as much as possible in the printing process. In two places, the outer circle of the plate cylinder is developed into a plane, as shown in Figure 3.3.
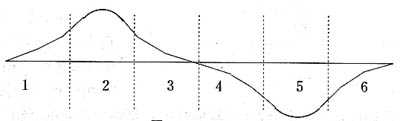
Obviously, there is no need to transfer graphics in the gap of the printing plate, so the requirement for string ink is the lowest. The surface of the printing plate is to be transferred with graphic and textural requirements. Combining the requirements of the surface of the printing plate for the ink stringing with the effect of the ink stringing ink on the ink string, the right and left reversing points of the ink stringing roller should be carried out at the notch of the printing plate, and the place with the largest amount of ink should be related to the printed one. The effective part of the printing of the effective part is opposite. If the image on the printing plate is close to the front half of the plate, the reversal point of the ink stringer can be moved to the trailing portion of the plate so that when the plate is reached, the tandem roller is in Zone 2 and 5 In the area, if the effective part of the printing is at the tip, the reversal point can be placed at the mouth of the printing plate. When the tip is pulled, the string ink amount of the ink string roller is already in Zone 2 or Zone 5. It can be seen from the above analysis that the change in the ink amount of the ink string roller directly affects the uniformity of the ink on the printing plate. The reversal point can only appear on the non-printing part of the printing plate, and generally it is in the gap of the printing plate. From this it can be seen that the ink roller is from left to right and the plate cylinder is rotated one revolution; the ink roller is from right to left, and the plate cylinder is rotated one more time. That is to say, the ink fountain roller reciprocates one cycle, and the plate roller rotates two times.
There is a large amount of ink in the ink stringer, and the effect of the ink stringing is good, but the ink amount of the ink string should not be too large, because the axial rotation of the ink string roller actually depends on the friction and ink. Friction generates heat, the temperature increases, the viscosity of the ink decreases, the imprint is easily deformed, and the emulsification of the ink is easily caused. The larger the ink volume, the worse the distribution inhomogeneity, as shown in Figure 3.4.
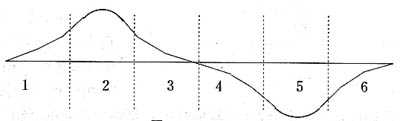
Therefore, the amount of ink is not too large. When the ink amount is too small, the ink cannot be opened axially, and the effect of uniform ink cannot be achieved. Therefore, the ink amount must be moderate. From the perspective of the ink string ink, the thinner the ink layer, the easier it is to evenly mix.
The size of the ink string is directly related to the graphic text. The smaller the area of ​​the graphic, the smaller the amount of string ink required; the larger the area of ​​the graphic, the greater the string of ink requirements. Therefore, the amount of ink string required for the bright-tuning part is small, and the amount of string ink required for the dark-toned part is large, and the amount of string ink required in the field is the largest.
When printing a packaged product, especially when printing some lines, it is sometimes necessary to simultaneously print several colors on one color group. At this time, the stringing roller cannot be allowed to move, that is, the amount of string movement is adjusted to zero.
At present, most of the ink on the machine uses reversed-phase ink, that is, the ink rollers roll from top to bottom, one to the left, and one to the right at the same time. As a result of such a string, the maximum amount of ink stringing overlaps, the minimum point also coincides, and the effect of ink stringing is not good. If the maximal points cross each other and the minimum points also cross each other, the uniform ink effect is better. This is the so-called phased ink.
The roughness of the surface of the ink fountain roller is very high. If the surface of the ink roller is too large, the effect of uniform blackening will be significantly worse. The accuracy of the surface of the ink roller is an important standard for factory inspection. Under normal circumstances, it must go through the grinding process.
The ink conveyed by the ink roller is ink, not water, so its surface should be oil-repellent and water-repellent, which can prevent the water from returning to the ink path and cause the ink to emulsify.
4. Uniform ink roller. The uniform ink roller has the following functions:
(1) Beat the ink in the circumferential direction This is the main function of the uniform ink roller. Theoretically, the ink layer thickness transferred to the surface of the printing plate should be uniform. This requires the ink to be evenly distributed both axially and circumferentially.
(2) Transferring ink and changing the distribution of ink Ink rollers As a bridge between ink rollers, it is necessary to transfer ink. The greater the number of rollers, the less ink is dispensed onto each roller and the fewer the number of rollers. The more ink is dispensed onto each stick, the effect of changing the ink distribution can be achieved by changing the number of rollers.
(3) It can make up for the processing and installation error of the ink roller The ink roller is all rubber rollers. When they are under pressure, they can be in close contact with other hard rollers to complete the ink transfer.
(4) Shock Absorption Because of the unevenness on the surface of other hard rolls, there are vibrations on the surface during movement. The results of these factors are converted into the elastic energy of the uniform ink roller. When it comes into contact, it is released, and when released, it is vibrated. And shock absorbed.
(5) Safety function Since the surface of the uniform ink roller can be compressed and deformed, when the foreign matter enters the ink path, the surface of the uniform ink roller is greatly deformed, while the surface of the other hard roller is not deformed, so as to avoid the damage of the hard roller. The movement of the uniform ink roller is driven by the friction of the ink roller. From the point of view of ink transfer, there should be no slippage in the place where it contacts. That is, the maximum static friction force of its rotation should be far greater than the frictional resistance or the viscous force of the ink that hinders the rotation of the other parts.
5. Heavy roller. The role of heavy roller is:
(1) Reliable contact between the ink distributor roller and the ink distributor roller. In fact, the heavy roller presses on the surface of the uniform ink roller, and the amount of vibration of the uniform ink roller is transmitted to the heavy roller. Due to the heavy weight of the heavy roller, its speed is very small, which is in accordance with the law of energy conversion, as shown in Figure 3.5. It can be clearly seen in the actual process that after the heavy roller is mounted, the vibration of the ink roller is significantly reduced.
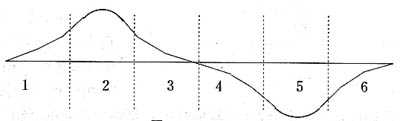
(2) Change the role of ink path and ink distribution. This effect is actually present with the uniform ink roller, as shown in Figure 3.6.
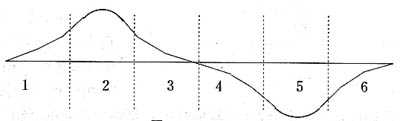
The heavy roller on the left is not in the ink transfer line, so it can only change the ink distribution. The right roller is located in the ink transfer line, so it plays a role in changing the ink path. Since the heavy roller participates in the ink distribution and transfer process, it is not allowed to destroy the uniformity of the ink. From this point of view, the surface of the heavy roller must be clean.
Ningbo Wellcome Trading Co., Ltd. , https://www.huike-homecare.com