The automatic fault detection system is a new type of auxiliary equipment. This kind of equipment is designed to actively look for possible problems on the printed pages during the printing process. There are mainly two types of automatic fault detection systems - "sampling" detection systems and "100%" detection systems. The technology used by the sampling inspection system is similar to that of the drum observation system. In fact, this type of inspection system only adds extra software to the drum observation system. A video camera is fixed on a beam with an engine and equipped with a flash device. In a series of printing processes, the system can constantly scan and move from one marked place to another mark each time the flash takes pictures. During this time, the marker for each position was scanned, but only a small number of markers were captured by the camera after flashing. Each marked print image is compared with the main image in memory. Any difference can be displayed on the screen to report to the operator and issue a warning. The system is very good for the observation of the drum image, because after all, the operator can see the image in a small area every time. However, for the automatic quality inspection system, it seems that it is sometimes possible to pick out the problems in the printing, and sometimes it cannot. In other words, this system works intermittently. The 100% roller observation system uses a completely different approach. There is still a need for a crossbar fitted with an engine and permanent installation of several cameras throughout the length of the drum. These cameras are usually of the line scan type. This means that instead of using a flash to take a snapshot of the print, the camera uses a continuous illumination system to sample samples one row at a time in the length direction of the drum. When the roller rolls and the printing is completed, the system samples the next line of samples. The retrieved sample information is continuously compared with the main image stored in the memory. The main image is composed of print information having the same length as the print product and the same width as the drum length. Once the 100% detection system detects something wrong, then they not only match in the length direction of the drum, but also in sync with the speed of the printing press, it can always detect the quality of the pixel in the corresponding position. Can it be applied to flexo printing? It is clear that the versatility of the use of flexographic printing is the key to the success of this printing method, and it is where it has enormous potential for development. This property requires that any kind of automatic quality inspection system has to have the flexibility to be able to handle a variety of applications. Variety of Selective Printing Lengths In flexographic printing, variations in print length are not an obstacle to 100% automatic quality inspection systems. As long as the length of the print is entered before starting the test, the system will automatically select the main image of that length. Diversification of printed materials Since flexographic printers can print on different materials, automatic quality inspection systems have the need to handle the same materials. Unlike the scintillating light illumination system, the continuous fluorescent illumination system used in the 100% automatic detection system can handle transparent and opaque films, paper, cardboard, metal foils, and a variety of materials that are laminated into thin sheets. In fact, any can be softened. Printer-printed substrates can all be tested. The lighting system used includes diffuse reflection and transmitted light. The diffuse reflection is using two fluorescent tubes next to the camera on the roller, one on each side so that the camera can see the "line." The light that the camera receives is the light that is scattered back from the drum, not the light that is directly reflected back. Diffuse light illumination is the main lighting system and it is extremely effective in observing problems. If the printed substrate is a transparent or translucent film, the inspection system at this time needs to install an additional fluorescent tube directly under the roller. The light penetrates the roller and causes the camera to see the “lineâ€. This method is extremely effective for the detection of film products. It is also known that the illumination system is a specular reflection system, still using a fluorescent tube, but this time it should be properly arranged so that the reflected light just enters the camera. This method is very effective for the detection of fabrics or prints with raised surfaces. The variety of inks used The inks used in flexo printing are varied, solvent-soluble, water-soluble, and metallic toners, etc., regardless of the use of that ink is not a problem for the detection system. All can be easily handled. The machine's width detection system can easily adapt to a wide range of printing sizes in flexo printing, from narrower rollers to just 2 meters wide rollers, and rollers with a width of more than 2 meters. To accomplish this task simply add more cameras. A narrower drum requires only two camera systems, while a wider drum may require 3, 4, 5, or even 6 cameras to mount them on a rack that spans the drum. Of course, in any machine, the various drum width ranges used can be covered by 100% of the observed range. The speed of the machine, whether in theory or actually the highest printing speed has been increasing. As machines reach speeds of 365 meters per minute or more, automatic quality inspection systems are becoming more and more important. The latest automatic quality inspection system can easily handle the running speed of these rollers. In fact, it is precisely because of the application of an automatic quality inspection system that the printing speed can be higher until the error information received by the system becomes unacceptable. Just because of the addition of quality inspection equipment, the speed of the machine has increased accordingly. There are many examples of this. These systems increase the operator's confidence in increasing the speed of operation. When the printer is running at a high speed, the operator can freely observe around the machine. As long as the green "good" observation light is always on, printing will be in a normal state. Once the warning light turns red, the operator should stop immediately until the problem is solved. Pattern types brought by printing The pattern types introduced in flexographic printing are various. Patterns and wood grain effects found in decorative wallpapers have been problems for several years, but some detection systems are now able to handle these more complex effects. The current state of the technology is that any pattern that may occur in flexo printing can be detected. The type of failure 100% quality inspection system has the ability to find the normal faults that occur in flexo printing, such as ring white spots, squeegee bar marks, paper and paper strips, bubble marks, ring spots Quasi-and double-images. Some situations require extra high resolution For special applications such as security and pharmaceutical printing, additional line scans are required in the camera to achieve higher resolution. Makes particularly delicate stripes and loops of white spots can be detected. Testing of faulty samples that are typically provided by prospective purchasers of automatic quality inspection equipment helps ensure that cameras are selected for these applications. Types of line scan cameras Line scan cameras vary depending on the number of pixels that they can scan, such as 512 points, 1024 points, 2048 points, or 4096 points per scan line. The resolution of the entire drum of the system is determined by the number of scanning points per camera multiplied by the number of cameras divided by the width of the drum. With a resolution of approximately 0.2 mm, the entire drum has a good detection capability for general malfunctions. The detection of special applications typically uses a resolution of 0.1 mm for the entire drum. The location of the automatic quality inspection system The use of an automatic quality inspection system is not limited by the printing press itself. If the system is applied to an off-line machine, it will also have the same effect, such as slitting machine, embossing unit, film applicator. In fact, as long as the material is in any continuous processing process on the roller, the system can be applied. Is a sheet of paper or "white" form. In fact, through the application of the inspection system, it becomes possible to form a sorting machine capable of classifying a printed paper pile or a white paper pile into a good pile and a bad pile. The balance of testing in the printing section or in the post-processing section usually depends on the mixing of installed printing equipment and post-processing equipment, and how to use the major equipment that has been obtained to obtain the highest quality. If there are eight printers and three processing equipments, it is very effective to install 100% inspection equipment on the processing machines, which can save costs. Using a 100% Quality Inspection System Although there are many benefits from using a 100% quality inspection system, there are three main ways to use this equipment: First, as an early warning device, its detected failure Can be accepted by customers; Second, as a serious failure to eliminate equipment to ensure that serious failures will not come to the eyes of customers; Third, as a quality data collection and reporting tools. The use of an early alarm device as an early warning device sets the system to detect small faults that can be accepted by the customer. An amber warning light, an on-screen data report, and a fault display indicate that some error occurred. However, none of the system outputs was connected so that virtually no fault was identified or rejected. When the above warning occurs, the operator needs to check the information and decide whether or not to take any action. Because 100% of the material is being tested, the data in the record report is very detailed and you can see the quality of the current print. Use as a mark of waste and use of a change control system 100% of the fault detection system has the ability to track a single mark to a scrap point on the machine. The output may be connected to a labeller, diverter, ink marker device, or inkjet printer. There are many ways to organize the output connections, mainly depending on the needs of the application. In roll paper applications, the use of a labeling machine is the most common application. It can apply a mark on the edge of a failed roll. In the paper version of the application, according to the paper-rejecting device on the machine, the blank blank paper version will be rejected. When the system is used as this type of control, it is usually much worse than an early warning device system. Mixing of early warning/waste rejection systems In practice, the above two systems are often used together. Sometimes a 100% detection system does not have only one fault detection algorithm, if there may be four algorithms. In this case, two of them may be rejected for rough rejects and the other two for early warning. The operator can easily select and set through the program. Quality Data Collection and Reporting The 100% fault detection system can collect and store fault information for warnings and alarms. It can also be used for fault reporting and data collection. The information is usually collected into a database and entered into the existing PC network through the interface, so that the data can be analyzed from the printer. A typical report screen shows the position of the speed and failure in the transverse direction of the drum, as well as the type of catch failure. Scroll bars can help operators see early data and front data. At the end of printing, the print report will be automatically produced. Overall Benefits of 100% Fault Detection The advantages of a 100% fault detection system are already apparent when the task is initially undertaken, and it is often possible to find many more faults than we can imagine. Take appropriate steps to solve some of the problems that can be solved, then the system is dedicated to monitoring the process to ensure a consistent level of print quality. Listed below are the common advantages that are summarized: (1) Continuous, proactive observation - 100% roller, 100% of the time. (2) Ensure that consistent quality is observed, irrespective of the operator's experience or change of class. (3) Improve productivity by optimizing the speed and quality level of the press. (4) Provide early warning of impending failures. (5) Faults are displayed in color on the screen to quickly identify the nature and source of the fault. (6) When printing expensive materials, maximize its print throughput and reduce overprint. (7) Reduce the waste of expensive printing materials, minimize its use, reduce costs, and increase customer retention. (8) Improve the company's image and make it competitive. (9) Can be used in accordance with the requirements of the ISO9000 standard. (10) Easy to carry out short-term products
Waterproof Duffel Bag
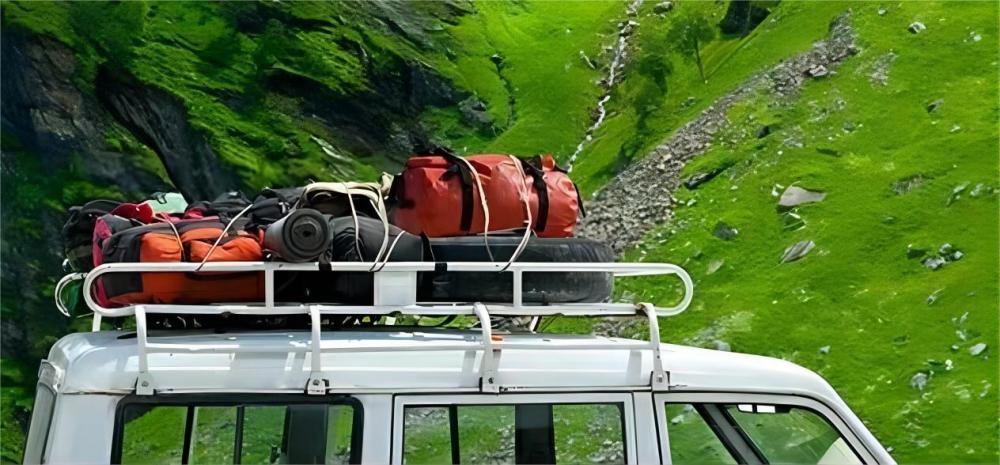
Whether it's a long-distance adventure, day rafting, or short weekend getaway, the DOING line of waterproof duffle bags is the perfect companion. Designed for both men and women. All your belongings will be protected from harsh weather with this bag.
â— This DOING waterproof Dry Duffel Bag adopts a high-frequency welding process, which has a comfortable feel and high-strength waterproof performance. At the same time, it is equipped with a detachable shoulder strap, which is one of the most powerful waterproof travel bags on the market; whether you are on a motorcycle trip or a long-distance self-driving trip, outdoor work or mountaineering adventure, it will follow you and take good care of you!
â— The DOING Waterproof Duffel Bag is made of high-density wear-resistant and tear-resistant material, and the PVC coating is sealed and waterproof, effectively blocking rainwater infiltration and providing dry storage space. Clean easily with a wipe.
â— Backpack mode and portable mode are convertible and ergonomic.
â— The Waterproof Overnight Bag has a large capacity, and there are multiple storage spaces inside to meet item storage needs.
Waterproof Duffel Bag,Waterproof Holdall,Water Resistant Duffel Bag,Waterproof Overnight Bag,Waterproof Duffel Backpack,Dry Duffel Bag
Danyang Doing Articles Co.,Ltd , https://www.doingarticles.com