Introduction
Metallographic analysis is one of the important methods for the experimental study of metal materials. The principle of quantitative metallography is used to determine the three-dimensional shape of the alloy structure from the measurement and calculation of the microstructure of the two-dimensional metallographic sample or the metallographic structure of the film. Quantitative relationship between alloy composition, structure and properties. The application of the computer to image processing has the advantages of high precision and high speed, which can greatly improve work efficiency.
Computer quantitative metallographic analysis is gradually becoming a powerful tool for people to analyze various materials, establish the quantitative relationship between the microstructure and various properties of materials, and study the dynamics of material organization transformation. The computer image analysis system can easily measure various parameters such as area percentage, average size, average spacing, aspect ratio, etc., and then determine the three-dimensional spatial shape, quantity, size and distribution of the features based on these parameters. It also establishes an intrinsic connection with the mechanical properties of the material, providing reliable data for more scientific evaluation of materials and rational use of materials.
The metallographic analysis report data mainly comes from the basic information of the National Bureau of Statistics, the State General Administration of Customs, the Development Research Center of the State Council, relevant domestic and foreign journals, and scientific research units of metallographic image analyzers. Report on the development status and prospects of China's metallographic image analyzer industry, the development status and prospects of the international metallographic image analyzer industry, metallographic image analyzer industry data, metallographic image analyzer industry benchmark enterprises, metallographic image analyzer industry Downstream, metallographic image analyzer price and sales channel price management, metallographic image analyzer industry investment strategy, marketing strategy, business management and competitive strategy are in-depth research, and focus on the prospects and risks of the metallographic image analyzer industry. Reveal the potential demand and potential opportunities in the metallographic image analyzer market, provide accurate market intelligence information and scientific decision-making basis for strategic investors to choose the right investment opportunity and strategic planning for the company's leadership, and also have great impact on the bank credit department. Reference value.
Test items
1. Welding metallographic examination;
2. Cast iron metallographic examination;
3. Heat treatment quality inspection;
4. Microstructure inspection and evaluation of various metal products and raw materials;
5. Inspection of low-fold defects of cast iron, cast steel, non-ferrous metals and raw materials;
6. Determination of metal hardness (HV, HRC, HB, HL) and grain size rating;
7. Determination of non-metallic inclusion content;
8. Determination of the depth of the decarburized layer/carburized hardened layer.
Testing process
Bulk sampling - test block inlay - rough grinding - fine grinding - polishing - corrosion - observation
The first step: the selection and interception method of the sample selection
Select the sampling part and the inspection surface. This process takes into account the characteristics of the sample and the processing technology, and the selected parts need to be representative.
The second step: mosaic.
If the size of the specimen is too small or the shape is irregular, it needs to be inlaid or clamped.
The third step: rough grinding of the sample.
The purpose of rough grinding is to flatten the sample and grind it into a suitable shape. General steel materials are often coarsely ground on grinders, while softer materials can be smoothed with a trowel.
The fourth step: fine grinding of the sample.
The purpose of fine grinding is to eliminate the deep scratches left during rough grinding and prepare for polishing. For general material grinding methods are divided into manual grinding and mechanical grinding.
The fifth step: the sample is polished.
The purpose of polishing is to remove the fine scratches left by the polishing and become a bright and non-marking mirror. Generally divided into mechanical polishing, chemical polishing, electrolytic polishing, and the most commonly used mechanical polishing.
Step 6: Corrosion of the sample.
To observe the microstructure of the polished sample under the microscope, metallographic corrosion must be performed. There are many methods of corrosion, mainly chemical corrosion, electrolytic corrosion, and constant potential corrosion, and the most common is chemical corrosion.
specifications
Metallographic analysis technical specification
1. TB 10212-2008 "Code for the manufacture of railway steel bridges"
2. DG/TJ08-2001-2007 (J10973-2007) Technical Regulations for Inspection and Identification of Steel Structures
3. DG/TJ08-804-2005 (J10616-2005) "Standards for the Inspection and Evaluation of Existing Building Structures"
4, GB/T 17455-1998 "metallographic replica technology for non-destructive testing surface inspection"
5, DNV ship classification specification "ship / high speed, light vessels and naval surface vessels - new vessels"
6. BS EN 1321-1996 "Destructive tests on welds in metallic materials-Macroscopic and microscopic examination of welds"
7, E45-05 "Standard Test Methodds for Determining the inclusion Content of Steel"
8. GB/T 3949-2001 "Test Method for Intergranular Corrosion of Marine Stainless Steel Welded Joints"
9, ISO 9015-1:2001 "Metal material weld destructive test - hardness test - Part 1: Hardness test of arc welded joints".
10, ISO 9015-2:2001 "Metal material weld destructive test - hardness test - Part 2: hardness test of arc welded joints"
11. BS EN 287-1:2004 "Qualification test of welders-Fusion welding-Part 1: Steel"
12. GB/T 5617-2005 "Determination of the effective hardened layer depth after induction hardening or flame quenching of steel"
13, DL/T 868-2004 "welding for assessment procedures"
14. DL/T 773-2001 "Spheroidization Rating Standard for 12CrMoV Steel for Thermal Power Plants"
15, EN 1320 "Destructive tests on welds in metallic materials-Fracture test"
16. GB.T6417.1-2005/ISO 6520-1:1998 "Classification and Description of Metal Melting Welded Joints"
17. GB/T13320-91 "Graphical Map and Evaluation Method for Metallographic Structure of Steel Die Forgings"
18, GB/T3098.1-2000/ISO 898-1:1999 "Mechanical performance of fasteners bolts, screws and studs"
19. GB/T 1172-1999 "Black metal hardness and strength conversion value"
20. GB/T11354-2005 "Determination of nitriding layer of steel parts and metallographic examination"
21, GB/T 2654-2008/ISO 9015-1:2001 "Test method for hardness of welded joints"
22, ISO 5817:2003 "welding - welding joints of steel, nickel, titanium and their alloys (except for high-energy beam welding heads) - quality classification of defects"
23, BS EN 1043.1:1996 "Destructive tests on welds in metallic materials. Hardness testing"
24, GB/T 19869.1-2005/ISO 15614-1:2004 "Steel, nickel and nickel alloy welding process qualification test"
25, JGJ81-2002 "Technical Regulations for Welding of Building Steel Structures"
26, GB/T 10561-2005 / ISO 4967:1998 "Determination of the content of non-metallic inclusions in steel, the rating chart microscopic test"
27, DL/T 674-1999 "No. 20 steel pearlite spheroidization rating standard for thermal power plants"
28, GB/T 9450-2005 "Determination and verification of the depth of carburizing and quenching hardening of steel parts"
29. GB/T 9451-2005 "Determination of the depth of the total hardened layer of steel or the depth of effective hardened layer"
30, GB/T 6394-2002 "Method for determination of average grain size of metals"
31. GB/T 231.1-2002/ISO 6506-1:1999 "Metallic hardness test - Part 1: Test methods"
32, GB/T 17394-1998 "Metallic hardness test method"
33, JB 4708 -2000 "Steel Pressure Vessel Welding Process Evaluation"
34. GB/T 4340.1-1999/ISO 6507-1:1999 "Metal Vickers hardness test - Part 1: Test method"
35, GB/T 224-87 "Determination of Decarburization Layer of Steel"
36, GB/T 226-91 "Steel low-fold structure and defect acid etching test method"
37. GB/T6401-86 "Metal phase method for determination of alpha phase content in ferritic austenitic duplex stainless steel"
38, GB/T 7216-87 "Gray cast iron metallography"
39. GB/T 9441-88 "Metallic Examination of Ductile Iron"
40, GB/T 13298-1991 "Metal Microstructure Inspection Method"
41, GB/T 13299-1991 "Metal Microstructure Evaluation Method"
42. GB/T 13302-91 "Method for evaluating graphite carbon in steel"
43. GB/T 13305-91 "Metal phase test method for α-phase content in austenitic stainless steel"
44, GB/T 1979-2001 "Structural steel low-fold defect rating map"
45, JB/T 5074-1991 "Low and medium carbon steel spheroids rating"
Major equipment
According to the process: cutting machine, grinder, sandpaper, inlay machine, polishing machine, optical microscope, video capture card, metallographic analysis software.
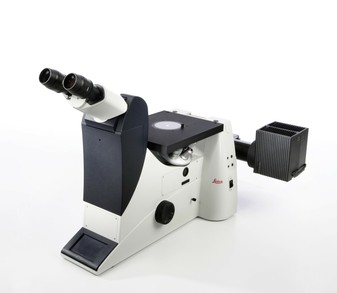
Do you need any professional hand mirrors? We have many styles about handheld mirrors. We also have many types of makeup mirrors, such as portable mirrors, magnifying glasses, travel mirrors, anti-fog mirrors, smart bathroom mirrors. Handle mirrors are also divided into many styles, different shapes, round lenses or squares, and the shape of the handle, we can also accept the customization of guests. The function is different, with or without lights, there are foldable types. In short, we also accept the design drawings of our guests for mass production. Makeup mirror must be convenient to open and close, so the use of aluminum alloy material will be easier to open and close than the plastic, will not damage the mirror surface, effectively prevent the mirror from crossing off, as for the lamp material can be selected ring frosted light bar, can be 360 ° fill light can also effectively protect the eyes. Outdoor makeup mirror is not convenient and makeup mirror is very portable, suitable for storage in the bag, allowing us to check their grooming anytime and anywhere, so that we can make up makeup in time can also act as a light source for taking photos and makeup repairs.
Hand Held Mirror,Hand-Held Makeup Mirror,Double-Sided Hand Mirror,Handheld Compact Mirror
Dongguan Powerme Tech. Co., Ltd. , https://www.powermetechs.com